Redi Services Improves Safety and Incident Reporting with Case IQ Case
Management Software
Redi Services
Streamlining workflow and eliminating repetitive tasks saves Redi Services $10,000 to $12,000 per year and helps to prevent incidents and accidents.
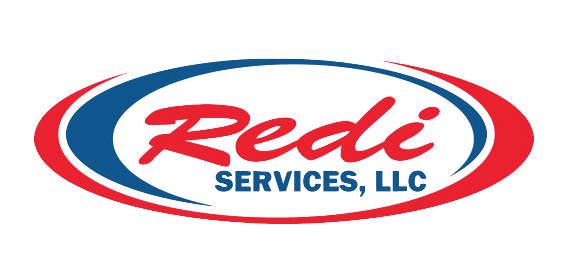
Redi Services Case Study Snapshot
Redi Services is an industrial services company, with 500 employees and headquarters in Wyoming and locations in Utah, Texas, Colorado and Nevada. Employees drive more than 10 million miles per year.
Incidents and accidents must be investigated and reported to OSHA, MSHA and other relevant authorities. The company must also track and document environmental incidents, such as spills, transportation issues and inspections.
"Redi Services saves $10,000 to $12,000 per year as a result of time saved entering health and safety incident data."
– Lance Norris, HSE Director
The Challenge
Historically the HSE team had been doing very little tracking and trending of incidents and accidents.
- They were missing the valuable opportunities for prevention that come with data reporting and root cause analysis.
- They began tracking incidents using Excel spreadsheets, which was inefficient and inconsistent.
- They transitioned to an Access database solution, but had difficulty setting up and maintaining it.
- Incident reports were inconsistent across the company.
- Having multiple people inputting information into the database was inefficient.
- Notification of incidents took too long and jeopardized the team’s ability to comply with requirements to report incidents within a 24-hour timeframe.
- There was no mechanism to notify stakeholders about incidents.
- The database was housed on an internal server, which put the system and the data at risk.
The Solution
Redi Services needed a cost-effective incident management solution that was easy to use and enabled consistent and fast reporting and messaging across the organization.
The HSE team needed:
- A single repository to keep all documentation in one place
- A way to eliminate manual tasks and notifications
- Automated notifications for stakeholders when an incident is reported
- A centralized system for easier completion of OSHA 300 logs, MSHA 7000-1 forms and other regulatory filing
- A structured workflow with built-in automation for alerts and notifications of incidents so that they could meet the 24-hour notification requirement and avoid penalties
- A powerful reporting tool to provide an overview of incidents and do root cause analysis
- A time-saving tool that allowed local HSE managers to focus on coaching and training, rather than investigating incidents
- A mechanism for tracking corrective actions and follow-up
The Result
Since implementing Case IQ in 2017, Redi Services has seen dramatic improvements in efficiency and risk management.
- HSE managers now enter incidents into Case IQ quickly, often within 20 to 30 minutes of notification, well below the 24-hour requirement.
- Automated notifications alert the executive team immediately upon the submission into Case IQ.
- The executive team is able to conduct root cause analysis in a timely manner, with all relevant supporting documentation easily accessible.
- Customers get quick written notification of incidents as soon as the executive team has conducted their review.
- Completing OSHA 300 logs and MSHA 7000-1 forms is quick and efficient with all documentation centralized and accessible.
- Redi Services saves between $10,000 and $12,000 per year in time by eliminating repetitive information entry.
- Redi Services has access to valuable current and historical incident data for analysis and prevention.
- The company has implemented safety programs to reduce the number of vehicle incidents.
Read the Full Case Study
Redi Services is an industrial services company, with headquarters in Wyoming and locations in Utah, Texas, Colorado and Nevada. The 500-employee company serves the oil and gas, power distribution and mining sectors with industrial insulation and scaffolding, painting and coating, transportation, hydro blasting and excavation, electrical and HVAC, and industrial maintenance services.
With such a broad range of services distributed across the western US, Redi Services employees spend much of their time on the road, clocking more than 10 million miles per year. And that mileage comes with significant risk for incidents and accidents, with the company averaging about 250 of them per year. And while most of them are minor incidents, they all must be investigated and some of the more significant incidents are reported to OSHA, MSHA and other relevant authorities. Other issues that must be tracked and documented include environmental incidents, such as spills, transportation issues, policy violations and inspections.
The Challenge
When Lance Norris, HSE (Health, Safety and Environment) Director, joined the company 10 years ago, Redi Services was smaller, with less onerous requirements for incident investigation and reporting. Even so, the company was doing very little tracking and trending of incidents and accidents, missing the valuable opportunities for prevention that come with data reporting and root cause analysis.
They began with a low-cost solution, tracking incidents using Excel spreadsheets. “We found that to be pretty cumbersome for what we’re doing and there was a lot of inconsistency across the company,” says Norris. “When you’ve got people doing it in five different states…incident reports did not look the same across the company.”
Redi Services soon transitioned to an Access database solution, but had difficulty setting up and maintaining it. “It’s a powerful tool, it’s just that you have to be a programmer to run it,” says Norris. “And I just didn’t have the time to learn how to do it in addition to my day job.”
The system was also inefficient. “The person filling out the report would go in and fill it out, and I would go in and make changes… and people would forget to put stuff in,” says Norris. “So there was a lot of work and rework, and just really a lot of effort.”
Neither the Excel nor the Access solutions provided a way to notify stakeholders about incidents. “When we had an incident, I’d call the Chief Operating Officer then I’d call the CFO then call the Operations Manager. And that was just hard and cumbersome,” says Norris. This manual method for notification of incidents took valuable time that the team needed to comply with requirements to report incidents within a 24-hour timeframe.
Final reports would be submitted to Norris, who would enter the data onto a spreadsheet. “We were entering in the same data two, three or four times in some cases, because then it was how the clients wanted it,” he says.
In addition, the database was housed on an internal server, which put the system and the data at risk.
The Solution
Redi Services needed a cost-effective incident management solution that was easy to use and enabled consistent and fast reporting and messaging across the organization.
They needed a single repository to keep all documentation in one place with secure access to case information for those who require it. Having all the incident information organized and centralized would make it easier to complete the OSHA 300 log, MSHA 7000-1 form or other regulatory filing, when required.
They also needed a structured workflow with built-in automation for alerts and notifications of incidents so that they could meet the 24-hour notification requirement and avoid penalties. “I was looking for an efficient system to make sure when we enter an incident, it sends an email to our executive team, so that everybody’s getting the same message,” says Norris.
The team needed a powerful reporting tool so that they could get an overview of incidents and do root cause analysis. Tracking corrective actions and follow-up was also important.
Ultimately, the HSE team needed an efficient system that eliminated manual tasks and saved time. “I wanted our local HSE managers to have more time in the field doing proactive coaching and training and those things that are more effective … versus reactive stuff like incident investigations,” says Norris.
The Results
Since implementing Case IQ in 2017, Redi Services has seen dramatic improvements in efficiency and risk management.
HSE managers now enter incidents into Case IQ quickly, often within 20 to 30 minutes of notification, well below the 24-hour requirement. Once an incident is entered, automated notifications alert the executive team immediately upon the submission into Case IQ.
The executive team is able to conduct root cause analysis in a timely manner, with all relevant supporting documentation easily accessible and customers get quick written notification of incidents as soon as the executive team has conducted their review.
Having all documentation centralized means that completing OSHA 300 logs and MSHA 7000-1 forms is quick and efficient. This also helps when cases involve legal action. “Two years after the incident, when I’m dealing with a worker’s comp claim or liability on an auto claim, I have all the data, all the evidence right there,” says Norris. “When the lawyer requests it years down the road, it’s easy to go in and print it out and send it off to them.”
Case IQ’s automated tasks save the HSE team hours of time every day, which saves the company money. “I would guess that it’s somewhere in the realm of about $10,000 to $12,000 a year that we’re saving in time through the entry and the double entry that we were doing. And that’s a rough estimate that I think is fairly conservative,” says Norris.
Redi Services has access to valuable current and historical incident data for analysis and prevention. Based on reporting in Case IQ, the company has implemented programs to improve safety. “We’ve implemented a ‘get out and look’ backing safety program and we put a lot more emphasis on defensive driving,” says Norris.
“I wanted our local HSE managers to have more time in the field doing proactive coaching and training …versus reactive stuff like incident investigations.”
– Lance Norris, HSE Director
Take the Next Step
Experience how a birds-eye view of your company's activities and results can help you better monitor emerging trends and risks. Want to know more about Case IQ's valuable insight?